What hardware should engineers prioritize for humanoid robot development?
What hardware should engineers prioritize for humanoid robot development?

A great humanoid robot should possess qualities such as being smooth in its movements, lightweight for energy consumption, affordable for widespread accessibility, powerful for efficient task execution, and flexible/adaptable to various environments and tasks.
The word ‘humanoid’ is on everyone’s lips, and rightfully so. The global market for humanoid robots could experience a compound annual growth rate (CAGR) of 46.5%, from $1.7 billion in 2023 to $36.1 billion by 2030, projected MarketDigits
Behind the buzz, however, lie significant technical challenges that must be addressed to see our shared dream become a reality. Weight, battery design, controllability, human-robot interaction, and power efficiency are all areas that have seen remarkable improvements in recent years. Yet they remain critical problems for humanoid robotics.
Rather than passively waiting for progress to happen, let’s dive headfirst into understanding these issues and exploring potential solutions together. In this discussion, we’ll explore the technical hurdles facing humanoid robots and how innovations like the Archimedes Drive can pave the way for overcoming these obstacles.
1 – Lightweight and Durable Design – Light and optimize actuators:
When we talk about humanoid robots, we’re discussing machines that are designed to resemble and mimic human movements and interactions. We want robots to be agile, able to move swiftly and with precision, just like a humans. This is where the optimisation of actuators, the ‘muscles’ of our humanoid robot, comes into play. Actuators are responsible for translating electrical signals into mechanical motion, enabling the robot to move its limbs and perform tasks.
Lightweight drives are essential in robot design, as they trigger a cascade effect of weight reduction. As each joint becomes lighter with a lightweight actuator, subsequent joints also benefit from reduced weight. Focusing on lightweight drives ensures that the arm’s weight decreases progressively along its length. The Archimedes drive, with its hollow cylinder design, provides an optimised solution for actuators, contributing to the overall weight reduction of the arm.
However, its hollow components aren’t the main reason why the Archimedes Drive is a lighter solution. Most high-performance speed reducers require a significant design buffer on top of their nominal torque output to be able to deal with shock loads, collisions, and vibrations, leading to increased torque requirements and thus a suboptimal design. The Archimedes Drive possesses the unique ability to enter into a sliding regime when subjected to conditions involving excessive torque. This slip mechanism acts as a safety feature, absorbing the excess forces, and thereby preventing catastrophic damage. Because this slipping mechanism mitigates overtorque situations, it eliminates the need for a design buffer and so extra size and weight. This not only makes robots like humanoids lighter but also enhances their efficiency, performance, and reliability, especially for applications where shock resistance is critical.
Output: Actuator optimization allows for a lighter construction with reduced material requirements, thereby enhancing both durability and agility.
2 – Efficient Power Systems – Advanced microchips and efficient actuators
The heavier humanoid robots are, the more energy they need to operate. However, there are options to make their power system more efficient.
Advanced microchips, also known as integrated circuits or ICs, play a crucial role in efficiently managing power consumption within the robot’s electronic systems. These chips are designed to regulate voltage levels, control current flow, and optimize energy usage across various components. By utilizing highly efficient microchips, power wastage can be minimized, and so overall efficiency maximized. This efficiency translates to longer battery life and reduced energy requirements, ultimately contributing to a lighter battery pack.
Following this context of lightweight battery design, selecting components that strike a balance between performance and weight is primordial. The Archimedes Drive is a solution for this need. Equipped with overtorque protection and precision control mechanisms, it offers very low energy losses compared to commonly used transmission systems, achieving efficiency levels of over 90%, while remaining compact and lightweight as composed of hollow cylinders (traction rollers or flexrollers). By using high-performance actuators (no backlash, smooth surface, continuous traction), we can improve the overall power usage of a humanoid robot.
Output: By combining advanced microchips with energy-efficient actuators, we can maximize the robot’s uptime while minimizing power consumption.
3 – Controllability and Transparency – Stiffness and zero-backlash:
In robotics, controllability refers to the degree to which a robot’s movements can be precisely controlled by its actuators. So, when we give a robot a command, it moves exactly how we want it to. Transparency, on the other hand, is about making sure that the humanoid robot responds to our commands quickly and accurately, without any delays or mistakes. A transparent actuator system is like a set of muscles that work well together. Helping the robot to move seamlessly and accurately.
One of the key characteristics of a transparent actuator system is its stiffness. Stiffness refers to the ability of an actuator to resist deformation when subjected to external forces (stay rigid, no bending, no wobbling). The planets of the Archimedes Drive are called Flexrollers. These Flexrollers act like very strong springs, generating high internal forces. These continuous internal forces result in an incredibly stiff design, resulting in predictable behavior. Resulting in precise and predictable behaviors.
Additionally, true zero backlash is essential for transparency in actuator systems. Backlash refers to the clearance or play between mechanical components, such as gears or linkages, which can introduce delays or inaccuracies in motion control. In this article, we wrote about the definition of ‘zero backlash’ and how it is often misused. Because all core working components of the Archimedes Drive are continuously in contact, it achieves true zero backlash. This results in robotic movements exactly the way we want, every time, under all circumstances.
Output: A transparent actuator system is characterized by stiffness and zero backlash, facilitating precise control and fluid interactions in various environments.
4 – Enhanced Human Interaction – backdrivability and noise reduction
Enhanced human interaction is about making sure that humanoid robots are designed to work well with people, keeping us safe and making it easy for us to communicate and collaborate with them. A need that is rising fast, as more companies are opting for humanoid robots in their facilities.
Backdrivability refers to the ability of a robot’s actuators to be easily manipulated by external forces, including those exerted by human operators. This property is crucial for collaborative robotics applications, where humans may need to manually adjust or guide the humanoid robot’s movements. As warehouse companies are facing a shortage of available labor for repetitive and dangerous jobs […]. They are exploring solutions to address this challenge, and one promising avenue involves the integration of humanoid robots into their operations. Putting more importance on the collaboration between humans and robots.
In industrial and domestic settings, noise generated by robotic systems can pose challenges, ranging from discomfort to potential health hazards. With the Archimedes Drive, engineers have a powerful tool for minimizing noise levels. The Archimedes Drive speed reducer by IMSystems generates noise levels under 50 dB, with minimum levels going below 37 dB, and a frequency mimicking that of white noise.
Output: to address human needs you must consider factors such as noise reduction and backdrivability.

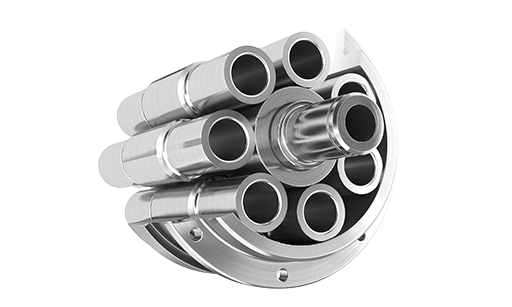
By using smooth, hollow cylinders (traction rollers or flexrollers) the Archimedes Drive presents a revolutionary solution for optimizing actuators in humanoid robots.
Instantaneous movement: With the traction rollers the Archimedes Drive boasts a zero-backlash design. Ensuring that every movement is precise and instantaneous. The Archimedes Drive enhances the responsiveness and accuracy of the actuators.
Stiff system: The cylinder of the Archimedes Drive provides continuous tractive contact, minimising wear and tear on the components and enhancing the overall
lifespan of the actuator. This improves the performance and reliability of the robotic system, even under demanding operating conditions.
Energy saved and extended battery life: With reduced friction and mechanical losses, the Archimedes Drive minimises energy consumption, leading to the improved overall efficiency of the actuator system.
Smooth and Quiet Operation: Thanks to its tractive contact mechanism the Archimedes Drive operates smoothly and continuously. As humanoid robots will perform tasks regularly next to humans. Their movement should perform the minimum noise level possible for a more comfortable and conducive working or living environment.
Reliability for unexpected loads: The Archimedes Drive incorporates advanced overtorque protection mechanisms. This feature ensures reliable operation even in situations where unexpected loads or forces are encountered, enhancing the durability and longevity of the robotic system.
Undesired motion prevented: Through its traction rollers, the Archimedes Drive exhibits enhanced resistance to backdriving forces, preventing undesired motion or
displacement when external forces are applied to the actuator. This capability enhances the stability and precision of the robotic system.
Customisable Reduction Ratios: The Archimedes Drive offers flexibility in adjusting reduction ratios to suit specific application requirements very easily. This customisation capability allows engineers to tailor the actuator’s performance characteristics to meet the demands of various tasks and environments.